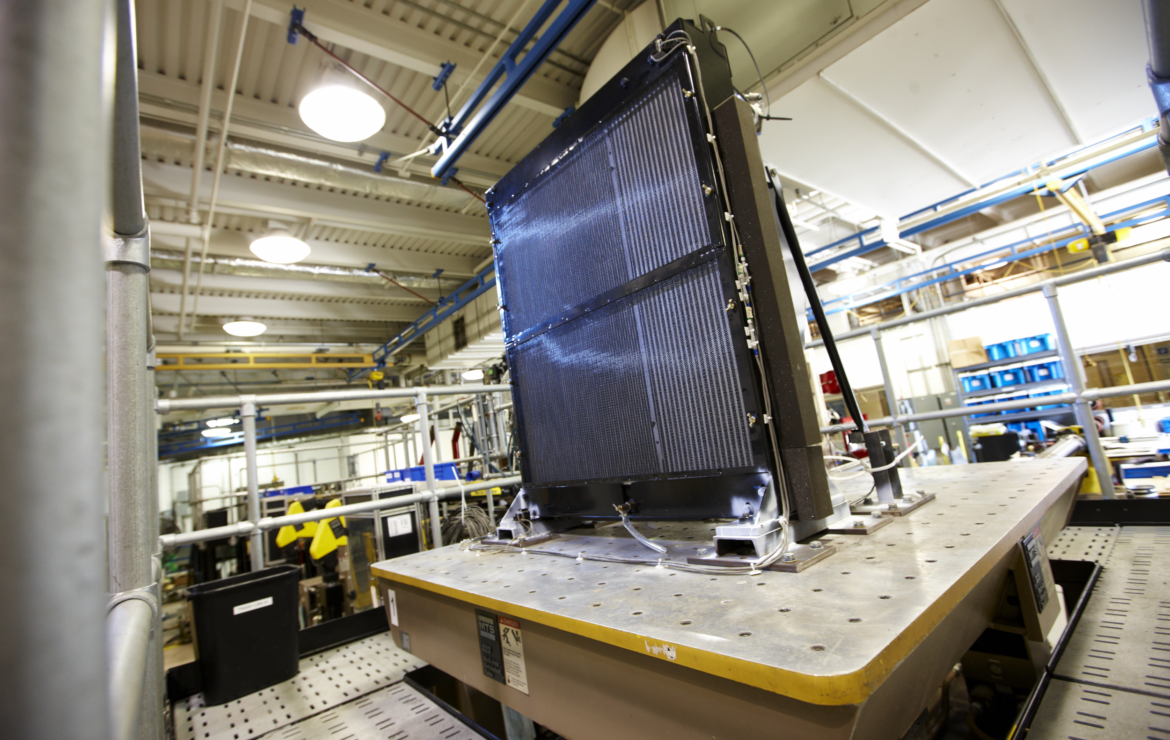
Behind the Scenes: Vibration Testing
Vibration testing has long been a consideration of vehicle design and engineering, essential for ensuring that components and systems can endure the stresses of real-world conditions. Initially involving simple mechanical setups to simulate road conditions, vibration testing has evolved significantly with advancements in vehicle technology. As the transportation industry embraces electrification, particularly with the rise of commercial electric vehicles (EVs), the demands on vibration testing have become more stringent. This includes addressing the unique failure modes in electronic components, such as PCB component failures, which were not prevalent in internal combustion engine (ICE) vehicles. Additionally, EVs have distinct vibration profiles due to weight distribution and battery placement, necessitating specialized testing to ensure reliability. Therefore, advanced vibration testing methodologies are now essential for validating that critical thermal management systems can withstand these demanding environments.
Modine is at the forefront of this evolution, developing state-of-the art vibration testing solutions tailored to the needs of commercial EVs, focusing on everything from engine performance to Battery Thermal Management Systems (BTMS), Electronics Cooling Packages (ECP), and passenger cabin comfort. Such comprehensive testing ensures that all components and systems are capable of handling the unique challenges posed by electrified and high-vibration environments.
To prepare designs for these rigorous conditions, Finite Element Analysis (FEA) is conducted prior to physical vibration testing. FEA is crucial of identifying potential structural issues. By pinpointing high-risks areas, FEA allows for targeted strain gauging and frequency sweeps to address these concerns and confirm the structural integrity of the system during testing.
Once FEA is completed, the Multi-Axis Simulation Test (MAST) system plays another key role in the vibration testing process. This advanced system replicates the intense operating environment that the thermal management system will face. The MAST system can reproduce a 6 Degree-of-Freedom motion profile – Longitudinal, Lateral, Vertical, Roll, Pitch, and Yaw – providing for dynamic and high-vibration conditions that accurately reflect those experienced by a heavy-duty commercial EVs. Unlike a full-vehicle proving ground test, the MAST system offers a more focused approach by testing only the component of interest. It also provides accelerated testing, as the profile rate can be increased compared to vehicle proving grounds. Additionally, the MAST system can reproduce vibration profiles recorded from proving grounds, ensuring that the testing accurately reflects real-world conditions. This precision reduces development timelines by eliminating non-damaging sections and facilitate continuous testing, ensuring that the component is thoroughly vetted to handle the high-stress environment.
Additionally, a single axis hydraulic actuator is used for specific directional testing. This actuator is configurable for vertical, horizontal, and angular orientations. This setup enables a variety of high-frequency vibration tests, including Sine, Random, Sine on Random, Road (Test Track), and Shock tests.
Considering BTMS as an illustrative example of how vibration testing is conducted to simulate the intense loading experienced in heavy-duty, high-use vehicles. The testing starts by mounting the BTMS on a vibration table, using vehicle-specific mounting points, frame structures, and isolators to closely replicate actual-use conditions. Hoses and associated hardware integral to the BTMS are included in the setup. The coolant system is filled and pressurized to simulate operational conditions, while the refrigerant system is pressurized with nitrogen. Throughout the test, accelerometers monitor critical areas such as the compressor and refrigerant lines to monitor their performance and detect any potential issues. The vibration testing is carried out according to either customer specifications or established industry standards. Typical test scenarios involve applying vibrations in various directions and frequencies to simulate real-world conditions experienced by the systems. Medium-Duty (MD) and Heavy-Duty (HD) trucks are tested following specific standards and agreements established with manufacturers. After completing the vibration testing, a comprehensive evaluation process is undertaken to ensure system reliability and performance. This includes checks for high voltage system integrity, coolant and refrigerant leaks, and functional assessments of key components like valves and sensors. These evaluation confirms that the BTMS can endure the high-vibration environments typical of commercial vehicles and maintain operational integrity.
As the commercial EVs market continues to evolve, Modine remains dedicated to advancing vibration testing methodologies. Investment in cutting-edge technologies and practices ensures that thermal management systems not only meet but exceed industry standards, delivering reliable solutions for future of commercial EVs. With over 100 years of experience in thermal management, Modine is the trusted partner to accelerate the transition to Zero Emission Mobility.